Generating design through
Digital Processes

Exploring the Fabrication Process of Continuous Formal Curvilinearity
Module 2
For M2 of Digital Design, we begin exploring the potential and possibilities of parametric design in the generation of geometric compositions; and practicing design refinement through iterations.
The latter half of the Module focuses on preparing the digitally designed model for physical fabrication.
I am interested in the mathematical and controlled modelling of organic forms and their translation from the digital realm into the physical.

Key concept
The key concept of the following exploration through digital design and fabrication is organic architecture, formal curvilinearity and curated circulations. The aim is to achieve a fluid composition, the form of curvilinear walls, pockets of varying spatial volumes and a continuously ascending or descending internal flow through the structure as a result of formal/geometrical organisation.
TASK a
Subtractive & Additive Processes



KEY ITERATION 1

-
This key iteration was chosen for its balance between 'blobbiness' and smoothness, the boolean difference extraction resulted in a very smooth and fully accessible flowing internal space. The morphing of curvilinear surfaces - walls, steps - throughout the structure, realizing the key concepts of formal curvilinearity and curated circulation.
-
By positioning the centroids of the metaballs on a spiral (curve), I was able to generate an organised arrangement of metaballs with full control of their volumes using a Gene Pool. Linear Array was used to control the thickness and density of levels between the isocurves generated through the Metaball(t) Custom component, these curves were then modified by increasing accuracy or smoothening which directly influenced the 'blobbiness' of the composition of the spiral metaballs.
KEY ITERATION 2
-
This key iteration was chosen for the superior sleekness in its surface, this iteration is the most successful in achieving the form of continuous and undulating curvilinear walls. It also features rounded openings, creating framed views. The sleekness also produces a highly diffused lighting that would permeate the structure's cavity. There is a more dynamic aspect to this iteration that stems from its compositional organisation.
-
A "Metaball Meshing" VB Script component by David Stasiuk was used to generate metaballs with a continuous mesh surface, that can be adjusted to produce simple enough mesh outputs to be converted to polysurfaces for boolean extractions. I also experimented with Weaverbird's Picture Frame and Stellation components to explore different ways that this metaball composition could be represented. Each metaball volume remains adjustable using Gene Pool.
-
The boolean difference extraction was rotated 180 degrees to gain a more accessible ground space/area.

KEY ITERATION 3

-
To generate this, a fairly simple, extruded metaball isocurve script formula was used; the same basic framework as the previous two, only now there is a controllable randomised abstraction component that can generate arrangements and patterns of metaballs really quickly within a 100x100x100 box. For this final key iteration, I was interested in constructing a formal dynamism, while combining two effects that were achieved within the previous key iterations: stepping and compositional organization of the metaballs.
Spatial Analysis of Task A Iterations
1

This key iteration most successfully creates a very unique spatial atmosphere when entered, through the geometries/form that continuously changes with each step, carved and morphing organically around the structure. Its curvilinear continuous and changing flow makes it a very interesting possible 3D printed model to physically translate and explore.
There is a very smooth flow through space, the entire internal space of the structure is accessible due to the spiral organization.
2

A carving of a lofted ring of compositional metaballs, resulting in another core-based structure. The arrangement and composition of the metaballs successfully create undulating curvilinear and continuous walls with rounded openings - creating another unique spatial atmosphere from its very smooth formal flow and composition.
Its perfectly generated connection between the different sizes and heights metaballs make it a very enticing possible 3D printed model to be able to explore physically.
A carving of a lofted ring of compositional metaballs, resulting in another core-based structure. The arrangement and composition of the metaballs successfully create undulating curvilinear and continuous walls with rounded openings - creating another unique spatial atmosphere from its very smooth formal flow and composition.
Its perfectly generated connection between the different sizes and heights metaballs make it a very enticing possible 3D printed model to be able to explore physically.
3

Exploring a 'combination' iteration, formal dynamism and hierarchy, a more dispersed & unique circulatory experience, open spatial experience through navigation.
This key iteration is a composite of abstract/randomised compositions to create a dynamic effect to the structure or final generated geometry. However, after a boolean intersection extraction, an integral factor that creates the dynamism in the form is lost as they are not attached. The intended design, therefore, lacks constructibility and does not achieve the complete desired effect when extracted.
SPACE/SCALE TESTS
Scripting: customized geometries
Grasshopper in Rhino 7 was used to script customizable forms to achieve the intended effects parametrically, which allowed for more control in producing each of the iterations.
Through exploration, I had discovered the Metaball tool in Grasshopper and knew instantly that it would be the best fitting structural base to parametrically manipulate and compose for my desired design outcome. Metaballs are organic-looking n-dimensional isosurfaces known for their ability to meld together when in close proximity to form a single contiguous object, this results in a 'blobby' appearance and is often used to model organic objects. I found their ability to fuse together exciting and saw the experiential fluidity potential these forms possessed absolutely worthy of exploration.
3d printing
When preparing a file for 3D Printing:
-
A geometry is first turned to a mesh and checked for open meshes - more polygons mean a better resolution, suitable for curvilinear forms, or exported as an .stl file.
-
It is important that a thickness analysis has been taken to ensure that there are no large areas under the minimum for a printer and to ensure the best possible translation of the design.
-
To ensure the most efficient (time, material and cost) printing process, proper orientation of geometries should be done within the printer software, a well-oriented geometry will require much fewer supports - cantilevers and holes flat on the ground.
-
The bottom side tends to have a rougher/different finish, in this file, all the geometries have been oriented uprightly as they all have very distinct exterior walls that are not to be sacrificed.

-
Completion time estimation from MakerBot Print: 13h40m for all three key iterations combined.
-
Material required: 100.75g.
TASK B
Sectional 'Waffle' Structures
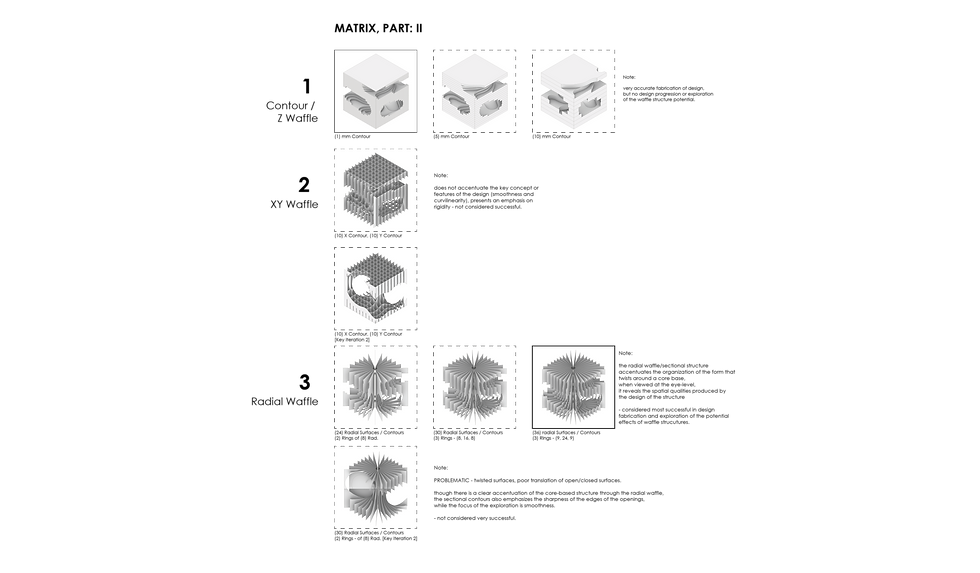
STUDY AREA
I have decided to continue with the first key iteration to explore the section & waffle structure, after a quick exploration of the effect of the different waffles on the first two key iterations (shown in Matrix: Part II).
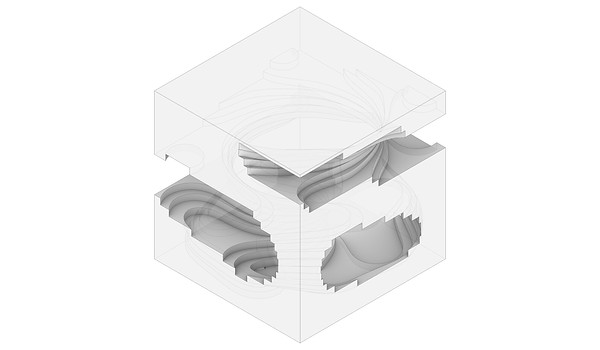
Through an assessment of the structural qualities of the first key iteration, and a familiarisation with the different waffling techniques, it can be seen that the vertical steps and curvilinearity only at XY-plane presented in this iteration makes it better suited for a z contour/waffle laser-cut fabrication if a perfectly accurate physical translation is what is aimed for.
However, the structure's spiral organisation and core-based design also mean that the radial waffle could potentially accentuate its radiating/ centrifugal structural qualities; while creating a possibility for further design elevation.
SECTION & WAFFLE STRUCTURES

The process of developing this technique was quite fascinating as each iteration of this design (increasing of contour thickness) resulted in a very streamlined but chunkier object/structure.
This iteration and sectioning strategy has been chosen as one of the translations of the design as it provides the more accurate fabrication of the design. Spatial qualities remain the same as the original model as this iteration of the Z/contour waffle produces a very high resolution and a very accurate translation of the design.
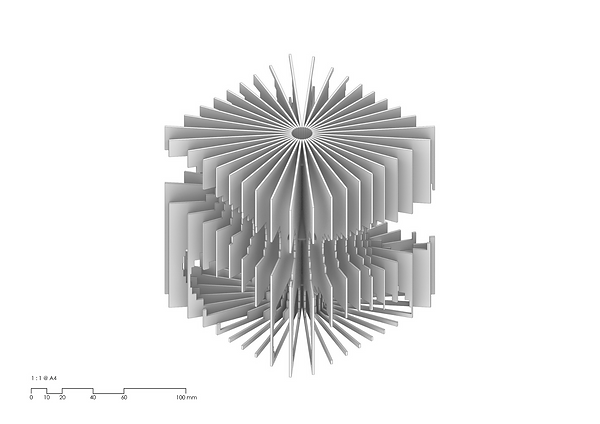
The process of developing this technique mainly involved the increasing of contours (increasing the curve division of the first ring), as well as, the adjustment of the rings and their allocations along the core of the radial waffle.
The radial waffle structure accentuates the organisation of the form that twists around a core base when viewed at the eye level, it reveals the spatial qualities produced by the design of the structure. Increasing to the highest amount of contours densifies the waffle while still maintaining its radiating structural quality, which presents a balance between the true fabrication of the original design and embracing the potential effects of a radial section/waffle structure.
SPACE/SCALE TESTS
Scripting: sectional structures
Grasshopper in Rhino 7 was also used to script and develop an exploration of the sectional/waffle structures of key iteration 1 from task A.
laser cutting
When preparing a file for laser cutting and physical fabrication:
-
It is important to ensure that no free space/distance between cut lines is less than the minimum for the material used, this number would depend on the specific sheet material and its thickness.
-
A single stroke or engraving font is most recommended, the laser would only need to go through it once, this would considerably decrease the amount of time needed to laser cut, here MecSoft_Font-1 was used for all etched text. All text tags are tucked in a discreet corner of each contour to ensure that each would be easily identifiable even after they are taken off the sheet.
-
To ensure that there would not be any space under the minimum distance between cut lines, only the top and bottom sides of the contours would lap, and to maximise material efficiency, smaller rings are tucked between unused space, and only 1mm of space allowance are between the sheets.
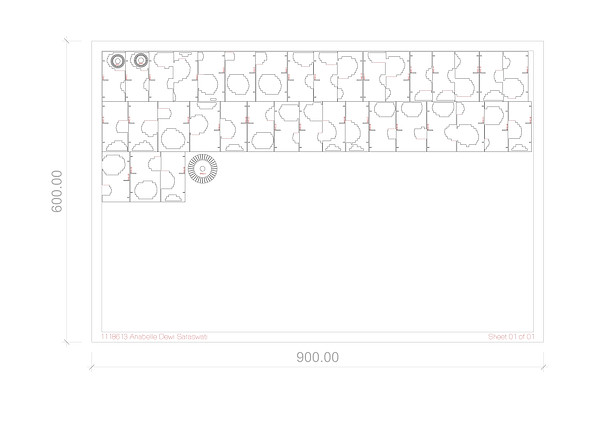
FINAL NESTING FOR RADIAL WAFFLE LASER-CUTTING FILE